by Espinseparators
Share
by Espinseparators
Share
Espin is a recent company but boasts know-how and long-standing, consolidated experience in the design, production and marketing of disc stack centrifuges.
Espin is a recent company but boasts know-how and long-standing, consolidated experience in the design, production and marketing of disc stack centrifuges, for different applications: dairy, beverage, oils and fats, engineering fluids and industrial waters, chemical and biotech.
Wherever it is necessary to separate liquids or remove ultra-fine particles, in order to recover a valuable substance or eliminate waste, disc centrifuges allow the best from the product, exceeding the limits of traditional filtration methods.
Starting from a careful analysis of the product and/or process needs and thanks to the solid knowledge and experience, Espin engineers and technicians seek and develop the most suitable solution for every need, in full compliance with the characteristics of the product to be treated.
Cutting-edge design, consistent and innovative research, top quality materials, a lean and flexible structure complete the picture of a solid and dynamic reality.
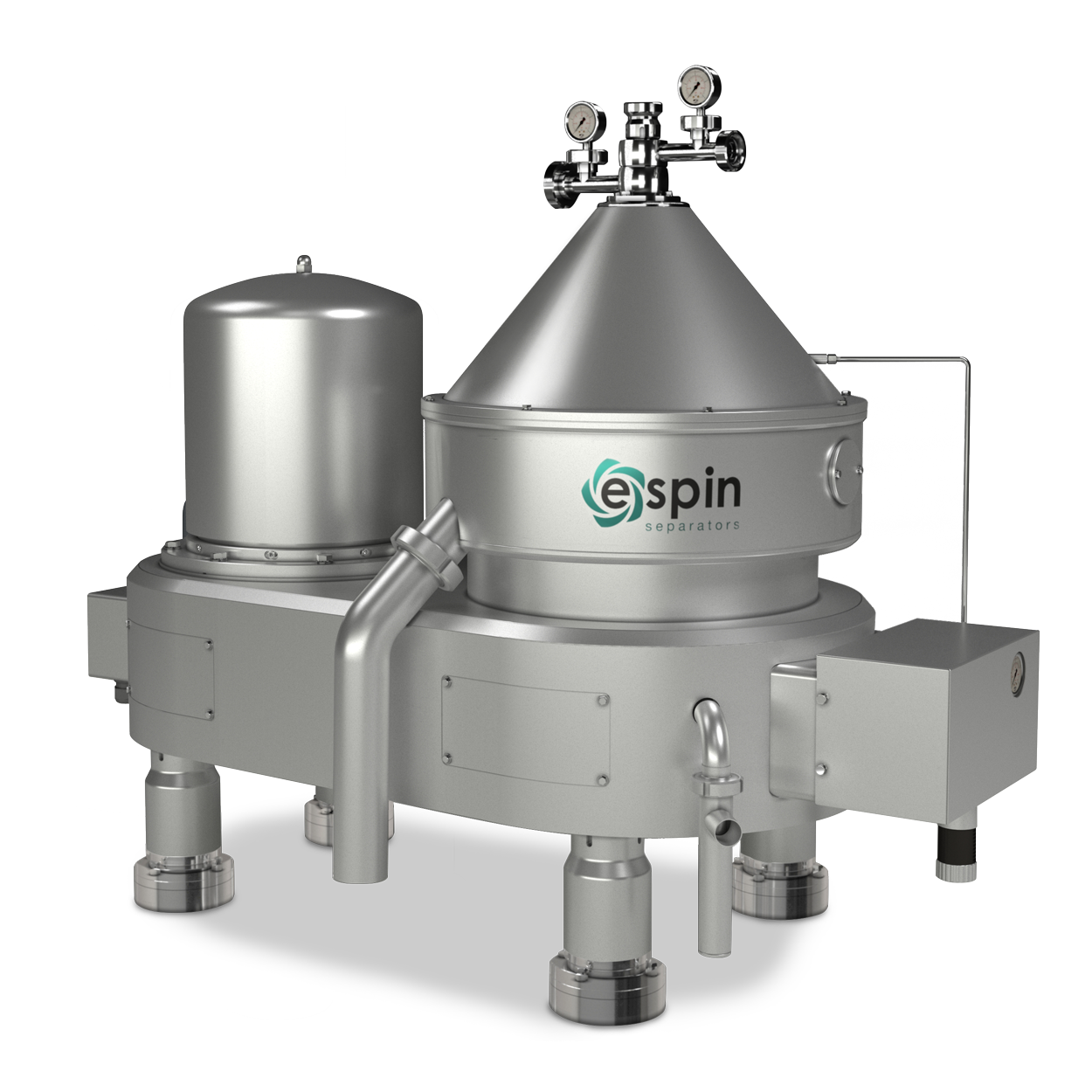
Espinseparators proposal for dairy industry
Continuous ongoing research has led us to develop a high-performance bowl, which allows top efficiency, a reduction of the installed electrical power and, therefore, energy consumption, resulting in lower operating costs. An optimized design also provides important advantages in terms of less spare parts and easier maintenance.
The range of products proposed by Espin includes both separators (for the separation of liquid phases of different densities and simultaneous ejection of solids) and clarifiers (for the separation of very fine solid particles from a liquid), all self-cleaning.
In particular, the Espin proposal for dairy includes:
- Warm milk and whey separators
- Milk and whey clarifiers
- Milk bacteria clarifiers.
Main features of Espin centrifuges:
bowl inox SUPER DUPLEX with very high resistance to mechanical stress and corrosion; parts in contact with the product inox AISI 304/316; cartridge-type vertical shaft; feeding system with soft inflow and hydrodynamic design to avoid damage to the product; hydraulic sealing to limit product oxidation and hermetic sealing to avoid CO2 losses; optimal performance.
Read the article on Tecnalimentaria.it
STAY UP IN LOOP